Variable shelling based on simulation results for lightweighting
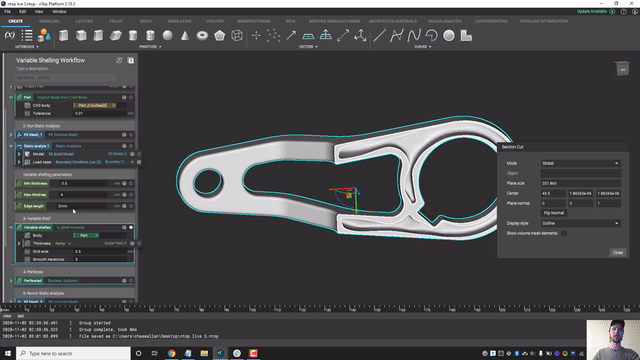
video:
Published on November 2, 2020
Applications
Key Software Capabilities
- Simulation
Using the results of FE simulations, you can control the thickness of a shelling operation. This way you can remove material only where stresses are lower and further reduce the weight of your high-performance aerospace or automotive structural components.
In this nTop Live, Chase Allan, Solutions Engineer at nTop, shows you how to apply a shell with variable thickness to a bracket in nTop. He creates a reusable workflow that uses a CAD file and simulation data as inputs and exports the shelled geometry as a STEP file.
Watch and learn how to:
- Apply a variable shelling operation to any CAD part
- Verifying the performance of the shelled geometry
- Export shelled geometry back to CAD as a STEP file
Download the files Chase used in this presentation here.
Related content
- CASE STUDY
Reducing weight to help win and withstand the rigors of a 24 hour Le Mans race
- ARTICLE
An nTop intern’s experience: Learning computational design and creating a lightweight drone
- VIDEO
Thermal Applications - The Hot Topics
- VIDEO
nTop CDS 2024: How COBRA Golf created the LIMIT3D irons
- CASE STUDY
Cobra Golf designed their LIMIT3D irons 50% faster with nTop