Flow management innovations: reducing pressure drop and energy

Written by Alejandro Carcel Lopez | Staff Application Engineer at nTop
Published on October 25, 2023
Applications
Key Software Capabilities
- Surface textures
- Topology optimization
Discover how nTop is improves flow management for turbomachinery in aerospace and defense applications.
Turbomachinery plays a pivotal role in the performance of aircraft engines, propulsion systems, and a wide range of defense applications. To meet the ever-increasing demands for efficiency, reliability, and performance, engineers are turning to additive manufacturing (AM) to breathe new life into both new and legacy turbomachinery components.
In this article, we will delve into flow management in turbomachinery for aerospace and defense applications. We will cover the impact of techniques such as design optimization, texturing, and perforations on turbomachinery, and discuss how nTop drives these advancements.
Challenges in flow management
Flow management poses a unique set of engineering challenges, such as:
Transient flow conditions
Many real-world applications don't operate under steady-state conditions. The flow can be pulsating, intermittent, or undergo sudden changes. Because of these transient conditions, engineers must consider additional variables such as temperature fluctuations, material stresses, and the dynamic interaction between different fluid phases. Failing to account for these variables can result in system failures or a considerable drop in operational efficiency.
Complex geometries
Modern equipment and systems, especially in aerospace and defense applications, often feature intricate and convoluted geometries. These complex shapes can significantly complicate the distribution of flow within turbomachinery components, leading to challenges such as unpredictable flow paths, the potential for undesired vortex formation, and difficulties in optimizing the design for optimal performance. Even a slight alteration in geometric design can have a cascading effect on overall flow dynamics. That’s why sophisticated design and simulation tools are needed for accurate results.
Designing for uniform outlet flow
Attaining uniform flow, especially at the outlet, is a fundamental objective in many flow systems. However, this goal becomes particularly challenging when there are multiple inlets and outlets within a system. Each inlet or outlet can introduce variations in flow rates, turbulence characteristics, and pressure conditions, making it a complex task to balance these differences and ensure uniformity at the outlet. Achieving uniformity often requires iterative design processes, extensive simulations, and meticulous attention to detail. As the number of inlets and outlets increases, the complexity of the task grows exponentially.
Tailoring flow characteristics for improved performance
In fluid dynamics, the direction, shape, and structure of flow are key in determining overall system performance. Two standout techniques have revolutionized flow management: flow guides and intricate fluid channeling systems.
Flow guides are precisely-engineered structures or components designed to steer fluid in a specific direction or pattern. Their primary objective is to optimize flow distribution, ensuring that the fluid adheres to the desired path with minimal resistance. When strategically designed and placed, flow guides can significantly reduce pressure drop within a system. This not only translates to reduced energy consumption, but also enhanced system efficiency overall.
Traditional manufacturing methods have long imposed limitations on the geometries achievable for fluid channels, constraining the potential for optimizing flow distribution. In contrast, additive manufacturing allows for greater design freedom. Engineers can envision and fabricate custom flow guides and intricate fluid channels with geometries that enhance flow distribution. These AM-fabricated channels can take on shapes and structures previously deemed non-manufacturable.
nTop can help you further accelerate the innovation process. By seamlessly integrating with simulation data and offering automated optimization processes, nTop enables engineers to iterate faster and identify the best-performing designs sooner. It allows for the direct import of results from computational fluid dynamics (CFD) tools to drive geometry directly from flow data, including essential parameters such as velocity fields.
Designing the flow: the role of aerodynamic textures
The smaller details also matter in turbomachinery design. Surface texture affects fluid flow behavior and characteristics. These textures — often intricate patterns or grooves — can be applied to various surfaces, including inlets, outlets, piping, and blades. This is where nTop can help, offering the capability to apply complex textures, ultimately improving aerodynamic efficiency and heat transfer.
These textures can:
- Reduce drag and pressure drop: Textures can streamline flow, reducing the frictional forces that lead to drag. This can in turn minimize the pressure drop across a component, enhancing efficiency and reducing energy consumption.
- Optimize fluid mixing: Textures can induce secondary flow patterns that promote better mixing of fluids. This is especially valuable in systems where homogeneous mixing of different fluids or fluid phases is crucial.
- Decrease vibrations: Controlled turbulence can minimize flow-induced vibrations, which can be detrimental to the longevity and efficiency of equipment.
- Control acoustic attenuation: By modifying the flow patterns and turbulence intensity, textures can help reduce or manipulate the noise generated by fluid flow.
Customizing filters with precision and efficiency
In fluid and particle management, filters are a first line of defense, tasked with blocking particles of specific sizes while allowing the fluid flow with minimal disruption. With nTop, engineers can design highly-customized filters with unparalleled precision and efficiency. nTop enables the creation of reusable workflows that seamlessly apply custom perforation patterns to any surface (or even within volumetric filters), improving filter design.
With nTop, you're not just editing basic parameters; you're controlling hole shape, size, spacing, and direction — down to the finest detail. Engineers can achieve:
- Optimized flow: By tailoring perforation or lattice patterns, engineers can optimize the balance between filtration efficiency and minimal flow disruption. This means that filters can be designed to capture particles effectively without hindering the flow.
- Adaptability: With reusable workflows, once a particular design or pattern is ready, it can be swiftly applied to other filter designs or systems. This reduces the design time and ensures consistent performance across various applications.
- Precision: With the ability to apply custom patterns, engineers can design filters that cater to precise requirements, be it particle size, flow rate, or any other parameter. This results in filters that are tailor-made for their intended application.
Harness the power of additive manufacturing with nTop
nTop gives engineers the capability to create intricate designs that were once challenging, if not impossible, with traditional computer-aided design (CAD) tools. With nTop, engineers can quickly refine designs using simulation data. This means faster iterations and consistently superior results. Moreover, nTop integrates with CFD tools, allowing designs to be influenced directly by flow data like velocity fields.
Adding to its design capabilities, nTop’s unique 3D texturing tools can be used to apply both functional textures or patterns to parts. These complex textures can enhance aerodynamic efficiency, reduce friction, and improve heat transfer.
Read through our guide on turbomachinery for the aerospace and defense industry for a deeper dive into what you can achieve with nTop and additive manufacturing.
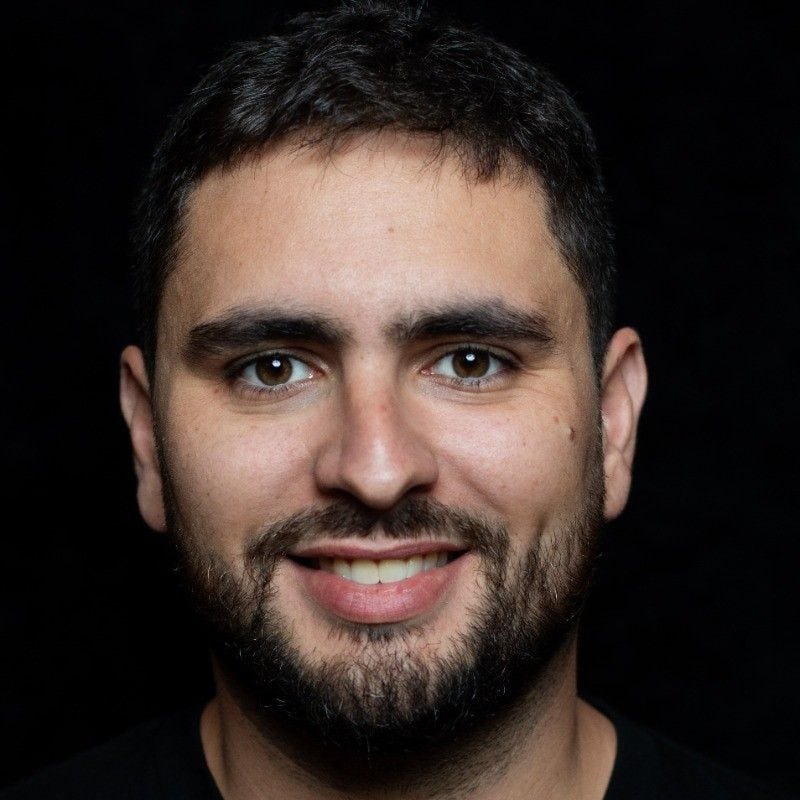
Alejandro Carcel Lopez
Staff Application Engineer at nTop
Alejandro is an MSc. Aerospace Engineer working in additive manufacturing and innovation for lightweighting and thermal management across several industries, mainly aerospace. He is experienced in the certification and qualification of aircraft propulsion systems and structures integration, design operational reliability, stress, thermal, and flow studies.
Related content
- VIDEO
nTop 2025 Nvidia GTC Presentation
- VIDEO
When your design changes, how fast can you respond?
- CASE STUDY
Replacing spacecraft supermaterial with high-performance lattice
- VIDEO
Creating a computational design workflow to lightweight drone panels with nTop’s new ribbing tools
- WEBINAR
Accelerating Product Engineering with Computational Design