Optimizing thermal management with conformal cooling to extend operational life
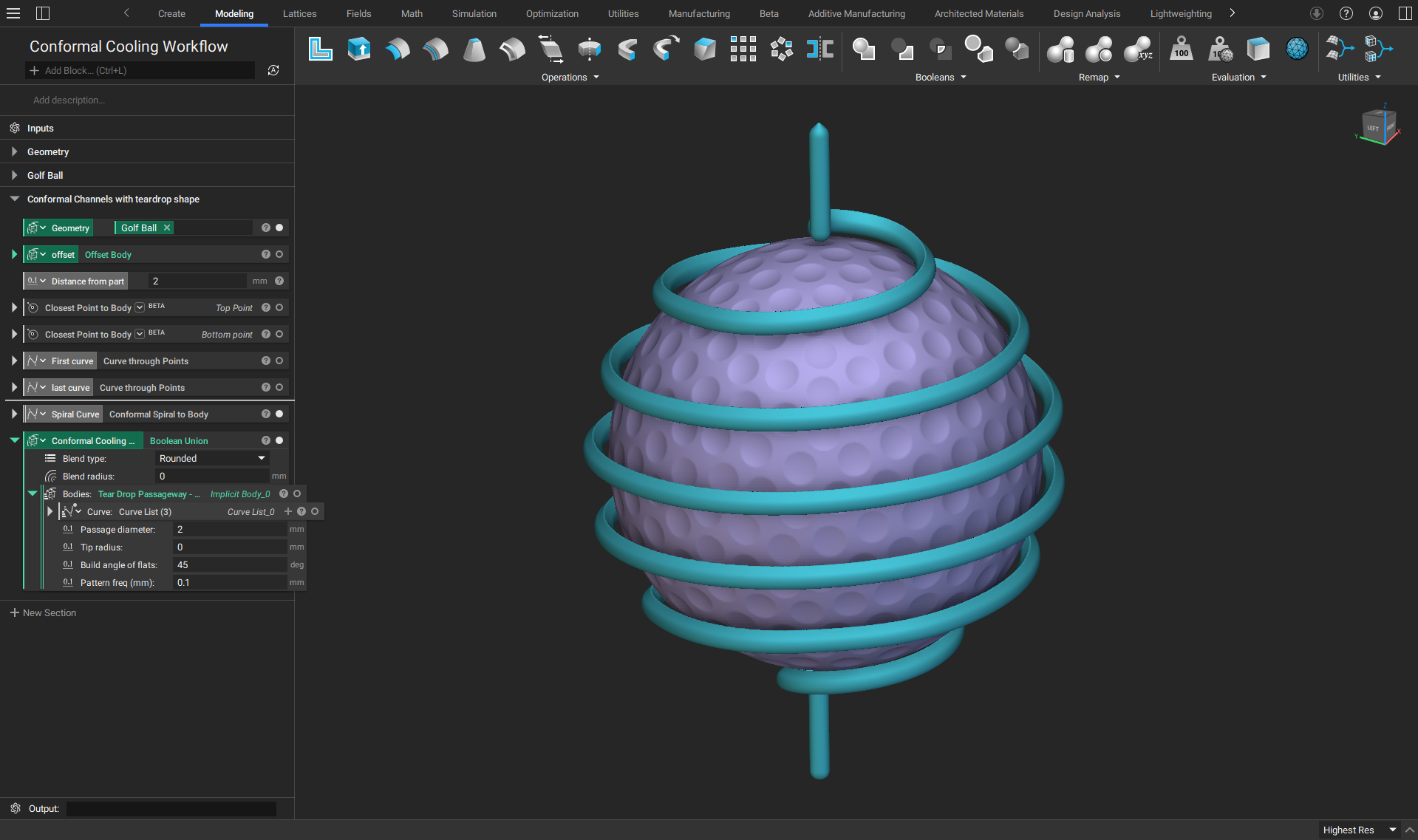
Written by Mandy Rosengren | Senior Solutions Engineer in Customer Success at nTop
Published on November 9, 2023
Applications
Key Software Capabilities
- Design automation
- Integrations
- Simulation
Conformal cooling can be an efficient thermal management solution. Learn how the intersection of additive manufacturing (AM) and nTop enables engineers to optimize heat dissipation and extend the operational life of components.
As technology advances, there are greater demands to produce high-performing, complex parts. Conformal cooling, enabled by additive manufacturing and next-gen engineering design software like nTop, can help overcome the challenges of conventional cooling systems with more effective heat dissipation, enhancing part quality and reducing energy consumption.
In this article, we’ll explore the benefits and techniques associated with conformal cooling and delve into its impact on modern manufacturing processes.
Conformal cooling vs traditional cooling
Unlike traditional cooling methods that rely on a collection of standard straight channels, conformal cooling takes on a more tailored approach. It involves creating intricately designed cooling channels that closely follow the contours and complex geometries of the components they are meant to cool. This design allows the cooling channels to maintain a uniform distance away from the mold, resulting in better heat dissipation and reduction in hot spots.
Relevance to injection molding and die casting
In injection molding and die casting, where temperature control is of great importance, conformal cooling can be beneficial. These manufacturing processes involve the rapid shaping of molten materials into intricate forms, often requiring the maintenance of specific temperature profiles for optimal results. Conformal cooling channels embedded within the molds ensure that heat is distributed evenly, reducing the risk of warpage and improving part-to-part tolerances. This leads to higher-quality parts and greater manufacturing efficiency.
Importance of heat management for part quality
Temperature variation, even by small degrees, can lead to defects, imperfections, and deviations from desired specifications. Conformal cooling not only minimizes temperature fluctuations but also facilitates faster cooling, reducing production cycle times. The result is improved part quality as well as increased throughput and cost savings — a win-win scenario for manufacturers.
Next, let’s explore the benefits that conformal cooling brings to industrial equipment and systems.
Unlocking the advantages of conformal cooling
Conformal cooling channels have the potential to improve component lifespan and part quality thanks to:
Improved heat distribution
By custom-designing cooling channels to match the topology of a component, engineers can effectively dissipate heat from critical areas. This targeted cooling minimizes temperature differentials and hotspots — a vital consideration in industries such as aerospace and defense, where component reliability is crucial.
As heat is evenly dissipated, the risk of deformations and defects diminishes, resulting in a more predictable and streamlined manufacturing process.
Minimized warpage, enhanced part quality, and reduced cooling time
By maintaining consistent temperatures throughout the part, conformal cooling helps prevent material warpage and deformation. This results in more consistent part-to-part tolerances and enhanced part quality. This heightened temperature control minimizes the risks of short shots and flow marks, further improving surface finishes and overall part quality.
Moreover, the uniform temperature distribution facilitated by conformal channels reduces cooling times, significantly accelerating production cycles. This efficiency boost translates to cost savings, increased throughput, and the potential for manufacturers to meet demand more effectively.
Additionally, minimizing waste becomes an inherent advantage, as there are fewer parts with defects in the production process.
Designing for efficiency
Creating effective conformal cooling solutions requires a meticulous approach. Here are the key design considerations that engineers should weigh when implementing conformal cooling solutions into their designs.
Following curvature
Conformal cooling channels are designed to closely adhere to the intricate contours and shapes of components. This precision is pivotal in achieving optimal heat transfer. Unlike conventional cooling methods that use a collection of straight channels, conformal cooling ensures that cooling is uniformly distributed — even in hard-to-reach areas.
By following the mold's curvature, these channels maintain consistent distance, eliminating uneven cooling, and improving the overall thermal performance of the system.
Additive manufacturing
Additive manufacturing unlocks greater design complexity, allowing engineers to produce these conformal cooling channels that are otherwise costly to produce. However, success requires careful consideration of manufacturing requirements.
When determining the suitability of AM for a specific use case, engineers must assess the volume of parts needed for injection molding/casting, the intricacy of the design, and the chosen material for the mold.
Because of the upfront cost of AM, the best use cases for conformal cooling include parts that will be produced in high volume, that contain complex designs (such as varying wall thickness), or are made of materials that require precise control in temperature.
Teardrop-shaped channels for AM
Teardrop-shaped channels are chosen primarily for their self-supporting structure. In traditional manufacturing, round holes, which are straightforward to produce, often require extensive supports when 3D-printed due to their overhanging areas, and these supports can be difficult to remove. In contrast, the teardrop shape eliminates the need for such supports, creating a superior surface finish and reducing potential issues during printing. This helps minimize waste, lowers material costs, and saves time in post-processing.
Efficient heat dissipation and introduction of turbulence
Efficient heat dissipation is the primary objective of conformal cooling. Engineers must focus on creating cooling channels that can evenly and rapidly remove heat from critical areas. Controlled turbulence within the channels is often necessary.
One way to achieve this is by applying additional surface roughness to the channels using advanced design software like nTop. By analyzing simulation results and leveraging computational tools, engineers can pinpoint areas where enhancing surface roughness can optimize heat dissipation and promote turbulence.
The application of these design considerations, when harnessed effectively, can result in conformal cooling solutions that offer superior thermal performance, reduced production costs, and enhanced overall system efficiency.
Shaping the future: the evolving landscape of conformal cooling technology
With the advancement of design and simulation tools, the effectiveness of conformal cooling channels will continue to improve. Here, we explore some of the future developments of conformal cooling design.
Utilizing TPMS structures
As design become more complex and demanding, it becomes more challenging to localize hotspots. Triply Periodic Minimal Surfaces (TPMS) structures can help increase the maximum surface area available and increase turbulence within cooling channels.
Increased surface area and turbulence not only ensure superior heat dissipation but also optimize thermal performance across the mold. Another added benefit of TPMS structures is that they are self-supporting, which reduces the need for additional support and simplifies the overall design.
Data-driven channel design
Future conformal cooling solutions must focus heavily on pinpointing and mitigating hotspots. Therefore, cooling channel paths driven by advanced simulations will be pivotal in achieving this goal, ensuring that even the most complex parts maintain temperature uniformity during the manufacturing process.
Using computational fluid dynamics (CFD), we can confirm that the flow rate and the temperature distribution are maintained evenly throughout the mold or adjust our designs accordingly to minimize low-flow regions and maximize heat transfer.
As computational techniques advance, this data-centric approach promises even more refined and efficient channel designs, significantly improving fluid optimization.
Iterative design processes
The future of conformal cooling is inherently iterative. With nTop, engineers can continue to refine designs based on real-world performance data and computational modeling. Once a part is designed, it undergoes simulations using a CFD tool.
Following this analysis, the design is imported into software like nTop to make necessary adjustments based on the CFD findings. This cycle of transitioning between CFD analysis and design refinements in nTop continues until the design reaches its optimal state. And, with nTop’s ability to create reusable workflows for a range of applications, this iterative loop can become automated.
This process not only saves time but also conserves material resources by reducing the need for multiple physical prototypes.
Additionally, advanced optimization tools can either assist in or autonomously generate initial conformal cooling channel structures, adhering to specified constraints and objectives. The combination of advanced software tools and selective use of additive manufacturing for some prototyping creates efficient and precise mold designs.
Harnessing the future of thermal management with nTop
Conformal cooling, with its ability to precisely regulate heat dissipation, reduce hotspots, and optimize mold performance, is changing how engineers approach thermal management in manufacturing processes.
With nTop, engineers can encode their expertise in a block-based visual programming environment, unleashing the power of design automation. They can scale their design processes through scripting and create reusable workflows, instantly applying design elements to different parts.
Want to discover more ways to nTop and additive manufacturing can help you improve your design process? Take a look at our resource center and discover the possibilities that await.
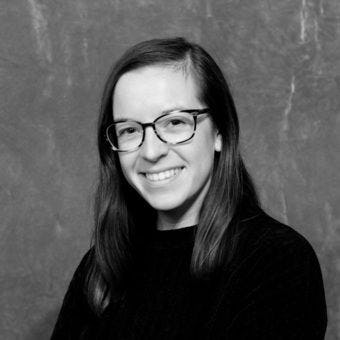
Mandy Rosengren
Senior Solutions Engineer in Customer Success at nTop
Many Rosengren is a Senior Solutions Engineer at nTop providing support on beginner to advanced content on simulation, topology optimization, latticing, automation, field-driven design, and DfAM. She has a background in mechanical engineering with a focus on additive manufacturing, and is experienced in designing automotive and aerospace parts, medical devices, prosthetics and consumer products within nTop.
Related content
- VIDEO
nTop 2025 Nvidia GTC Presentation
- CASE STUDY
Replacing spacecraft supermaterial with high-performance lattice
- VIDEO
Creating a computational design workflow to lightweight drone panels with nTop’s new ribbing tools
- WEBINAR
Accelerating Product Engineering with Computational Design
- VIDEO
nTop Siemens Energy at CDFAM NYC 2024