Wärtsilä optimizes industrial impeller for additive manufacturing

Written by nTop
Published on September 13, 2022
Wärtsilä's engineers redesigned the centrifugal pump impeller for additive manufacturing. Not only was the optimized turbomachinery component 44% lighter, but it was generated using an automated design process, enabling customization.
Centrifugal pumps and other turbomachinery are widely used in the energy and heavy industries for fluid transportation. At the heart of these devices lies an impeller, the rotating component that inputs energy into the fluid stream.
Industrial pumps may need to operate under a wide range of conditions. The impeller design is greatly affected by the fluid type, flow rate, and other working conditions and requires a high degree of customization. As a result, industrial manufacturers need to stock many individual parts to guarantee uptime.
For this collaborative project, engineers from Wärtsilä’s additive manufacturing center in Finland joined forces with nTop, SLM Solutions, and Oqton to create a digital workflow based on advanced engineering design and additive manufacturing technologies. The primary aim of this project was to replace the traditionally cast impeller.
The result was an impeller design that was 44% lighter and tested for 500 hours in an experimental setup under real-life conditions. In this design brief, we take a closer look at the key steps of the design and optimization process.
The benefits of additive manufacturing for turbomachinery

Photograph of the tested impeller after 500 hours of testing on a Wärtsilä laboratory engine.
This proof-of-concept design study focused on developing a design and manufacturing process for centrifugal pump impeller spare parts.
The selected turbomachinery component was a closed centrifugal pump impeller originally manufactured with metal casting. Its outer diameter was 200 mm, and the weight of the original part was approximately 2 kg.
Transitioning from a traditional process to additive manufacturing brings multiple advantages to Wärtsilä that are related to the impeller's performance and the factory management and operations.
Simplified supply chain
Typically, metal cast components have a lengthy lead time of a few months. On the other hand, additive manufacturing components can be ready-for-use in a few weeks. This capability reduces the need for keeping inventory stock. At the same time, additive manufacturing eliminates the need for expensive casting tooling, further simplifying the supply chain.
Lightweighting
Additive manufacturing also opens design optimization opportunities— specifically design lightweighting. A lighter impeller offers several performance advantages. For example, the impeller's reduced mass improves the rotor dynamics of the system, allowing it to achieve higher maximum tip speeds. It also reduces the load on the bearings, extending the life and improving the system's reliability.
Moreover, since the cost of materials is a significant portion of the total cost in additive manufacturing, reduced weight also means reduced manufacturing cost.
Impeller design and optimization
In this project, it was mandatory to keep the external shape of the component the same, so the optimization could only take place in the interior of the impeller. For this reason, the design team followed the “shell and infill” approach for structural design optimization.
Here are the steps the team's engineers followed:
- First, they performed a static analysis to determine the areas of maximum stress. The simulation results were later used to control key parameters using field-driven design.
- Then, they ran a topology optimization study to determine the optimal shape of the area near the hub of the impeller.
- Using the simulation results, they created a shell of variable thickness, increasing the thickness in the area where the stresses were higher.
- They filled the empty shell with a lattice structure. Like the shell thickness, the lattice beam thickness was controlled by the static analysis results.
- Finally, they combined the optimized hub, shell, and lattice and added additional features necessary for manufacturing, such as holes for powder removal and machining allowances.

The anatomy of the lightweight additively manufactured impeller.
By adjusting design parameters, like the thickness of the shell, the team created two design variations:
A “heavy” design with only 5% reduced weight. The design team opted for this conservative variation for the first iteration to evaluate the feasibility of the process.
A “light” design with 44% reduced weight. The goal of Wärtsilä’s engineers was to push the limits of the technology.
Customization of Industrial turbomachinery
It’s essential to point out that the team didn’t just design two impellers; they created a design optimization process. This means that a new optimized impeller can be automatically generated by importing a new CAD geometry and adjusting the boundary conditions of the simulation and topology optimization steps.
In other words, a new optimized model can be ready for review and manufacturing in less than 24 hours.
Design process automation is particularly important for this application as different centrifugal pumps require different impeller designs. nTop minimizes the engineering time needed to design custom industrial components, saving valuable engineering time and making the business case for additive manufacturing even stronger.

The optimization process reruns automatically by importing a new CAD body.
Process simulation and manufacturing
With the design ready, the next step of this digital workflow was process simulation and manufacturing.
Using Amphyon, Oqton’s metal additive manufacturing simulation software, the team created a compensated model that considered the distortion caused by thermal stresses, stress relief, and support removal. This process simulation and model compensation step contributed to keeping geometrical deviations below 400µm.
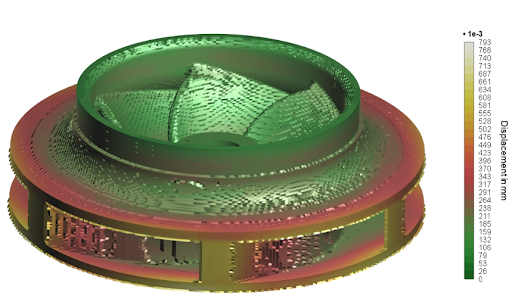
Process simulation in Oqton Amphyon for dimensional compensation.
An SLM®280 PS system featuring multiple lasers, closed-loop powder handling, and upgraded process control was used to manufacture the impellers. The material used was Inconel 718, a nickel-based superalloy designed to withstand extreme loading, temperature, and corrosion operating conditions.

The additively manufactured impeller before finishing with CNC machining.
Next steps
Wärtsilä’s engineers conducted a 500-hour bench test, monitoring the performance of the centrifugal pump with the additively manufactured impeller under different real-life conditions.
This pilot project is the first step for Wärtsilä's launch of its additive manufacturing center in Finland. The team plans to use the same methodology to scale the production of 3D printed impellers and other turbomachinery components for energy and marine applications.
Key takeaways
- The weight of the impeller was reduced by 44% without altering its exterior surfaces using the “shell and infill” approach.
- Reusable optimization workflows can automatically rerun on new impeller geometry, enabling customization of industrial components.
- The impellers were tested for 500 hours under real-life conditions, proving this digital workflow is suitable for use in an industrial environment.
nTop
nTop (formerly nTopology) was founded in 2015 with the belief that engineers’ ability to innovate shouldn’t be limited by their design software. Built on proprietary technologies that upend the constraints of traditional CAD software while integrating seamlessly into existing processes, nTop allows designers in every industry to create complex geometries, optimize instantaneously, and automate workflows to develop breakthrough parts and systems in record time.
Related content
- VIDEO
When your design changes, how fast can you respond?
- CASE STUDY
Replacing spacecraft supermaterial with high-performance lattice
- VIDEO
Creating a computational design workflow to lightweight drone panels with nTop’s new ribbing tools
- WEBINAR
Accelerating Product Engineering with Computational Design
- VIDEO
nTop Siemens Energy at CDFAM NYC 2024