DMG MORI redesigns robotic end-effector for additive manufacturing
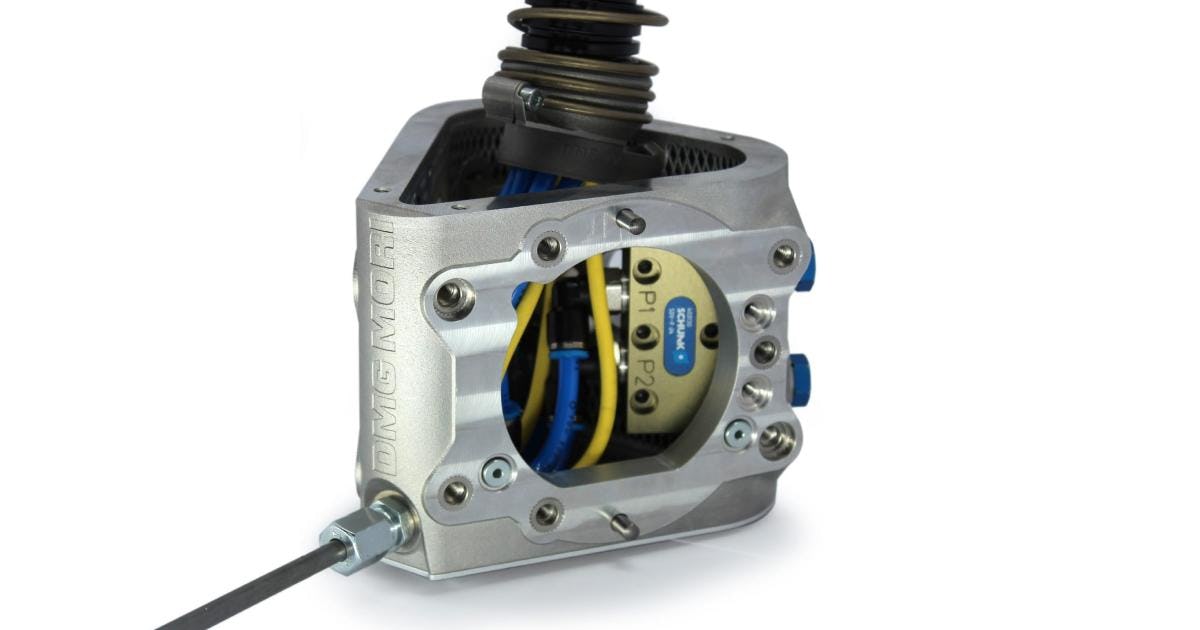
Applications
Key Software Capabilities
- Field-Driven Design
- Design automation
- Simulation
Summary
The engineers of DMG MORI’s ADDITIVE INTELLIGENCE team redesigned their Robo2Go head for additive manufacturing using nTop. The new design is 62% lighter, has 60% fewer components, and improves the handling precision of the robot by a factor of 16.

About: DMG MORI is a leader in metal-cutting manufacturing equipment, producing high-quality CNC machines for over a century. Over the past 20 years, DMG MORI has been investing in additive manufacturing, automation, and digitization.
- Industry: Manufacturing
- Size: 7,000+ employees
- Location: Bielefeld, Germany
- Product: 3D-printed end-effector
The project
Make theRobo2Go system more precise and efficient
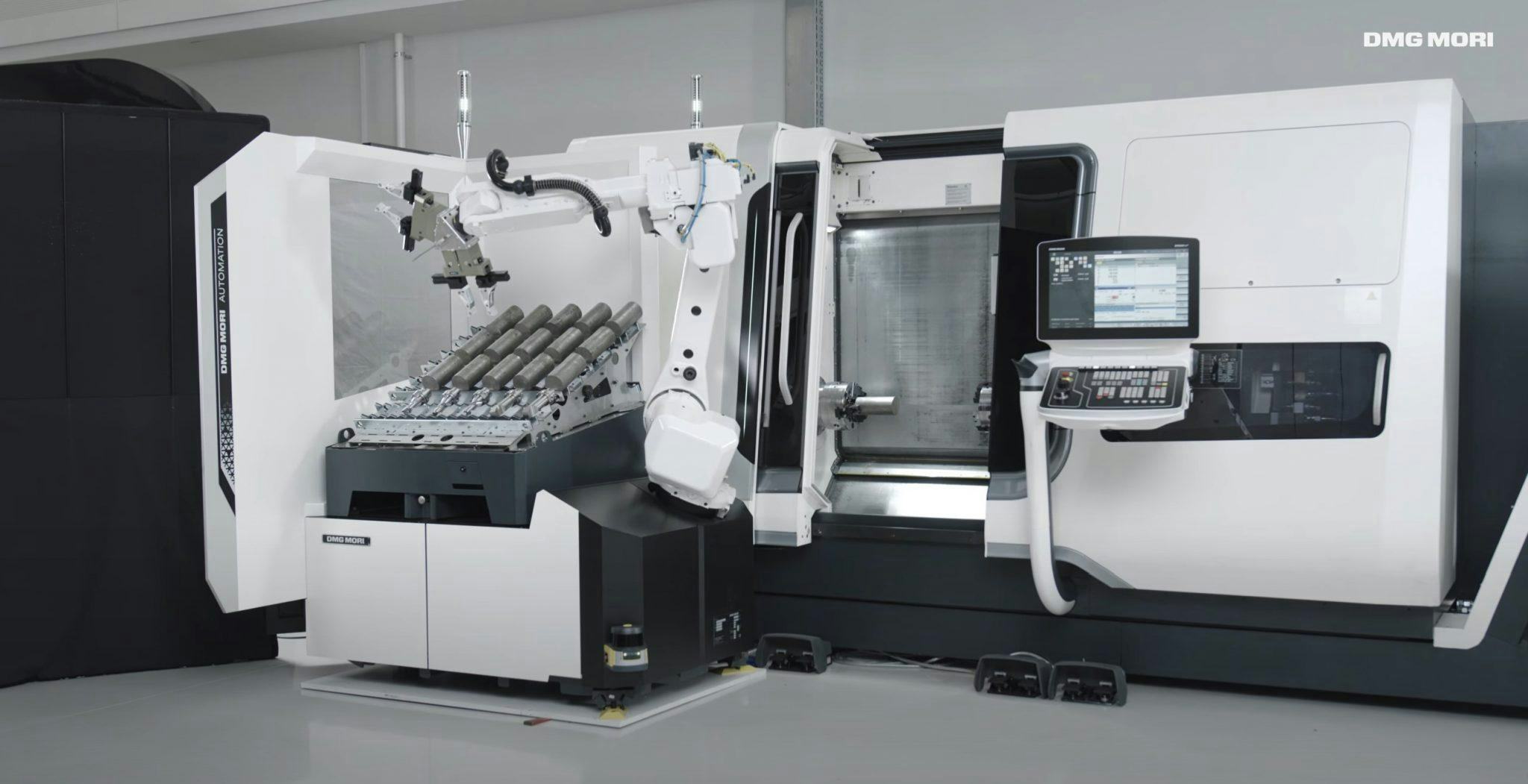
The DMG MORI Robo2Go 2nd Gen system on the factory floor. The redesigned part is the head that attaches the two end-effectors to the robotic arm. Source: DMG MORI.
DMG wanted to improve on the already successful design of the Robo2Go 2nd Gen. Their goal was to increase the precision of the machine and save valuable manufacturing and assembly time.
The challenge
Increase precision while saving manufacturing and assembly time
DMG MORI’s goal was to develop a lightweight design with the same external form factor as the original assembly but with a reduced number of components and a lighter weight. The original assembly contained 79 individual parts making tolerancing, precision, and assembly a challenge. Additionally, the stiffness and weight of this component limited the accuracy and maximum load capacity of the whole system.
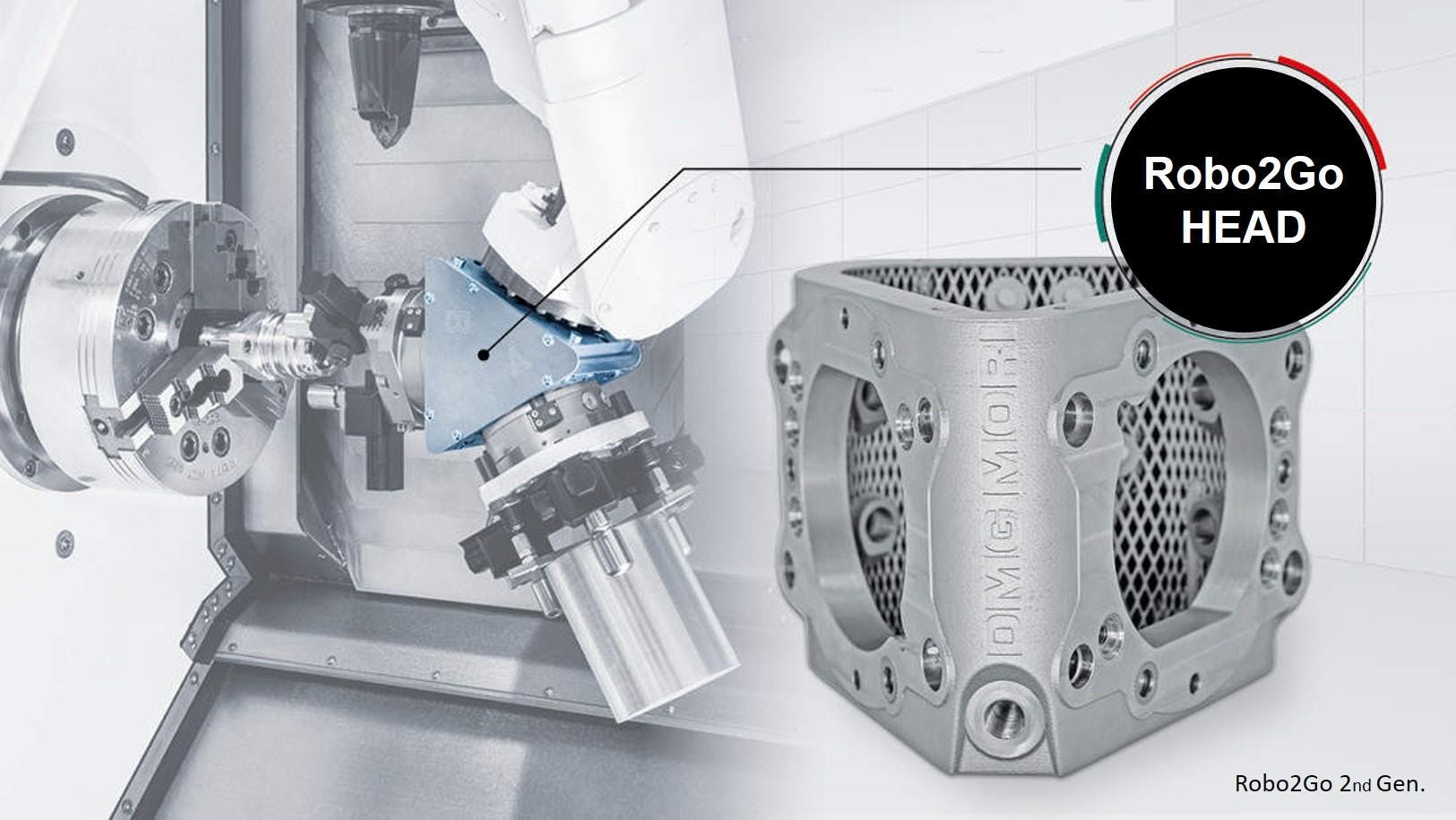
The original Robo2Go head (left) and the redesigned component (right).
The solution
DMG MORI used variable shelling and latticing to reduce the original design’s weight.
nTop’s Field-Driven Design capabilities made it possible to color code then shell each section with thickness driven by topology optimization to maximize stiffness. The team then filled the interior volume with a conformal lattice using nTop’s engineering simulation tools to rapidly iterate and select the optimal lattice. They also developed a reusable workflow so they can easily repeat the process in the future.
The results
62%
reduced weight
60%
fewer components
16x
higher precision
Why nTop?
nTop’s advanced capabilities allowed the DMG MORI team to create a powerful and unique additive design. The team improved the Robto2Go system’s bulky robot head by combining topology optimization with Field-Driven Design techniques and advanced lattice structures.
Topology Optimization
Since the DMG MORI engineers couldn’t alter the external form of the part, the results of topology optimization could not be used as the final design. However, they could use them to vary the thickness of the outer shell. This helped the team leverage some of the structural benefits of topology optimization without changing the part’s exterior.
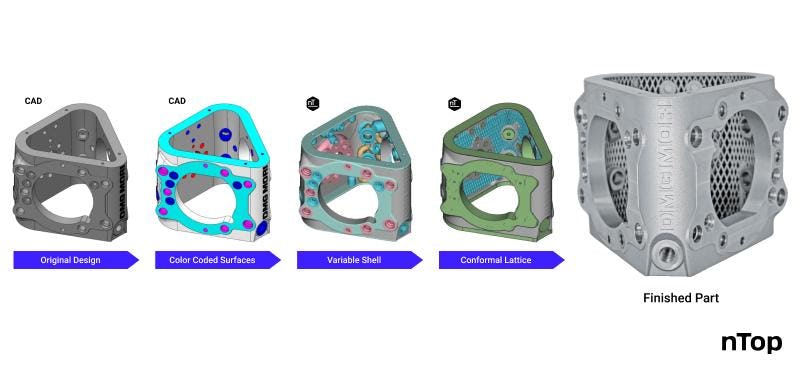
Overview of the design process - The surfaces of the original design were first color coded in CAD and then imported to nTop for lightweighting and optimization.
Latticing
DMG MORI filled the shell with a conformal lattice to increase the stiffness of the part and create a permanent support structure for additive manufacturing.
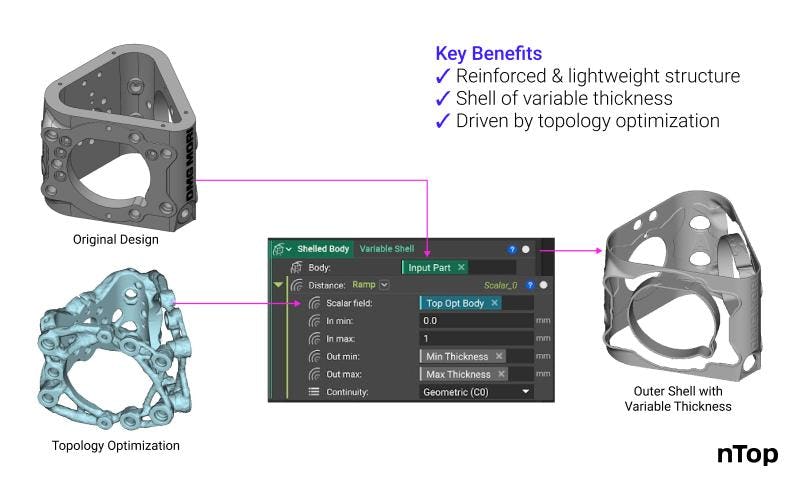
The topology optimization result drives the thickness of the variable shelling operation.
Integrated simulation tools
To identify the optimum lattice thickness, the team used nTop’s integrated simulation tools. This capability allowed them to automatically run multiple FEM and lattice simulations, quickly evaluate the results, and change specific parameters to optimize their design.
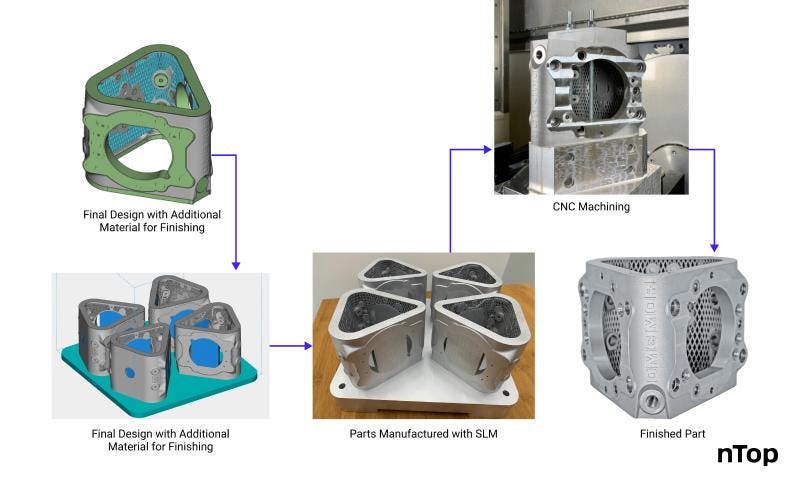
The final design was SLM 3D printed with additional offset material and then finished using CNC machining
Design automation
Instead of creating a one-off design, DMG MORI developed a robust and reusable optimization process. Using the color-coded surfaces of each subsystem of the imported CAD file as input, the team can automatically rerun their nTop workflow — even if the geometry changes due to design iterations or future projects.
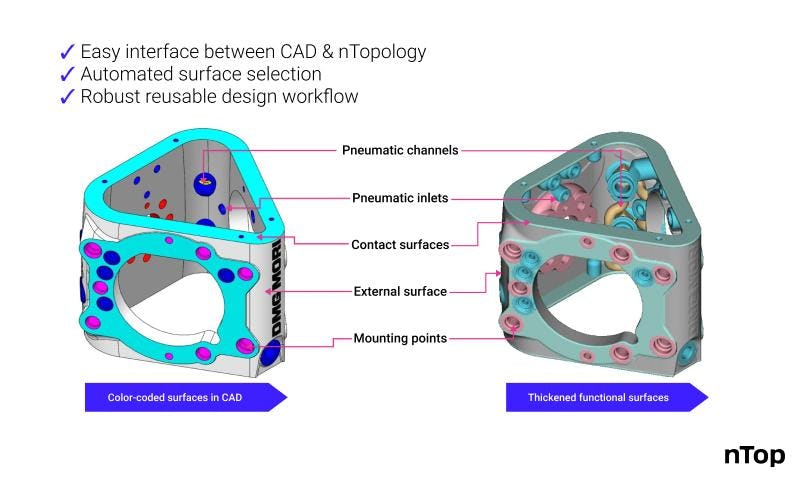
Color coding enabled the engineers to automatically select relevant surfaces in nTop and develop a robust and reusable design workflow to accelerate the design process.
Conclusion
Thanks to nTop, the DMG MORI team was able to create a lighter, simpler, and more precise Robo2Go head for additive manufacturing, creating reusable workflows that can be applied to future projects.
Related content
- VIDEO
nTop 2025 Nvidia GTC Presentation
- VIDEO
When your design changes, how fast can you respond?
- CASE STUDY
Replacing spacecraft supermaterial with high-performance lattice
- VIDEO
Creating a computational design workflow to lightweight drone panels with nTop’s new ribbing tools
- WEBINAR
Accelerating Product Engineering with Computational Design