Preziosa Francesco SRL and Add-it cut robot gripper weight 32-40%
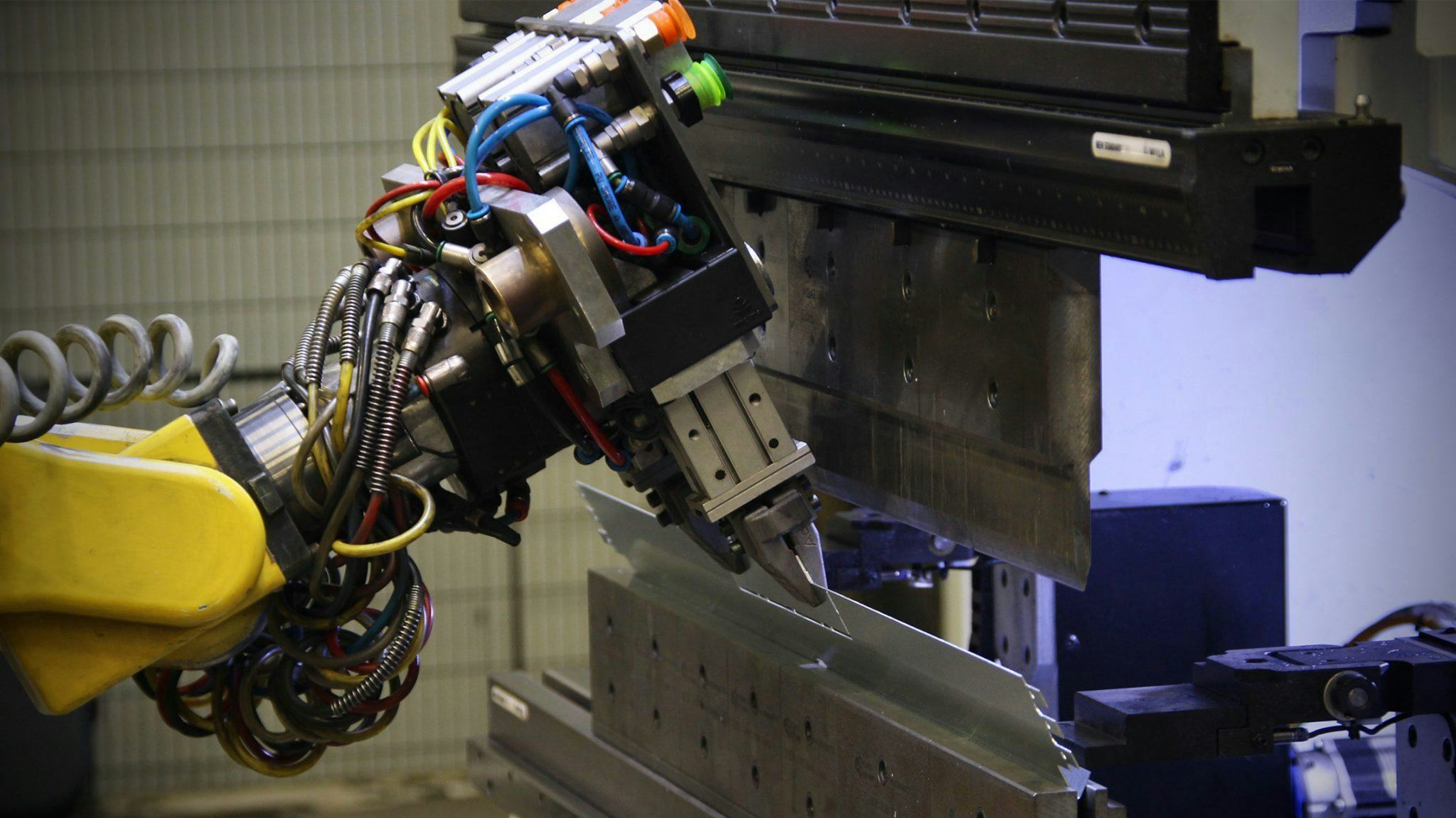
Applications
Key Software Capabilities
- Design automation
- Lattice structures
- Topology optimization
Summary
Preziosa Francesco SRL and Add-it redesigned the grippers of their press-brake-bending robotic cell for metal 3D printing. The final design was ready for use in just four days, increased system reliability, bypassed a supply chain bottleneck, and enabled lights-out manufacturing.

About: Preziosa Francesco SRL is a manufacturer of sheet metal cabinets based in Bergamo, Italy. They design and manufacture protective cabinets for gas and water meters, heating system manifolds, and more.
- Industry: Manufacturing
- Size: 1-25 employees
- Location: Bagnatica, Province of Bergamo, Italy
- Product: Metal 3D-printed robot grippers
The project
Re-design robot grippers for additive manufacturing
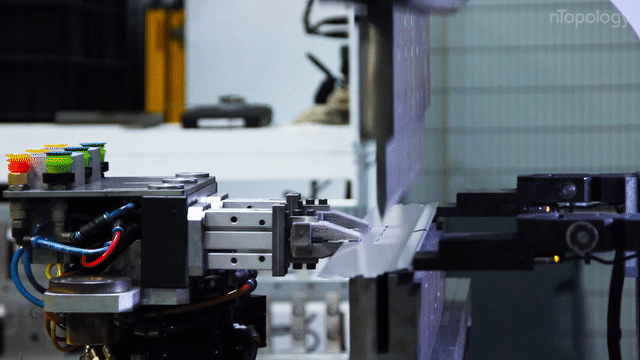
The new robot gripper design in action.
Robotic grippers are custom components that often need to be changed to meet the requirements of a custom sheet metal job. Preziosa Francesco SRL partnered with Additive Italia (Add-it, for short) to redesign their robot grippers for metal additive manufacturing. Add-it is a design consultancy specializing in simulation-driven engineering and generative design.
The challenge
Design reliable grippers that could be produced fast
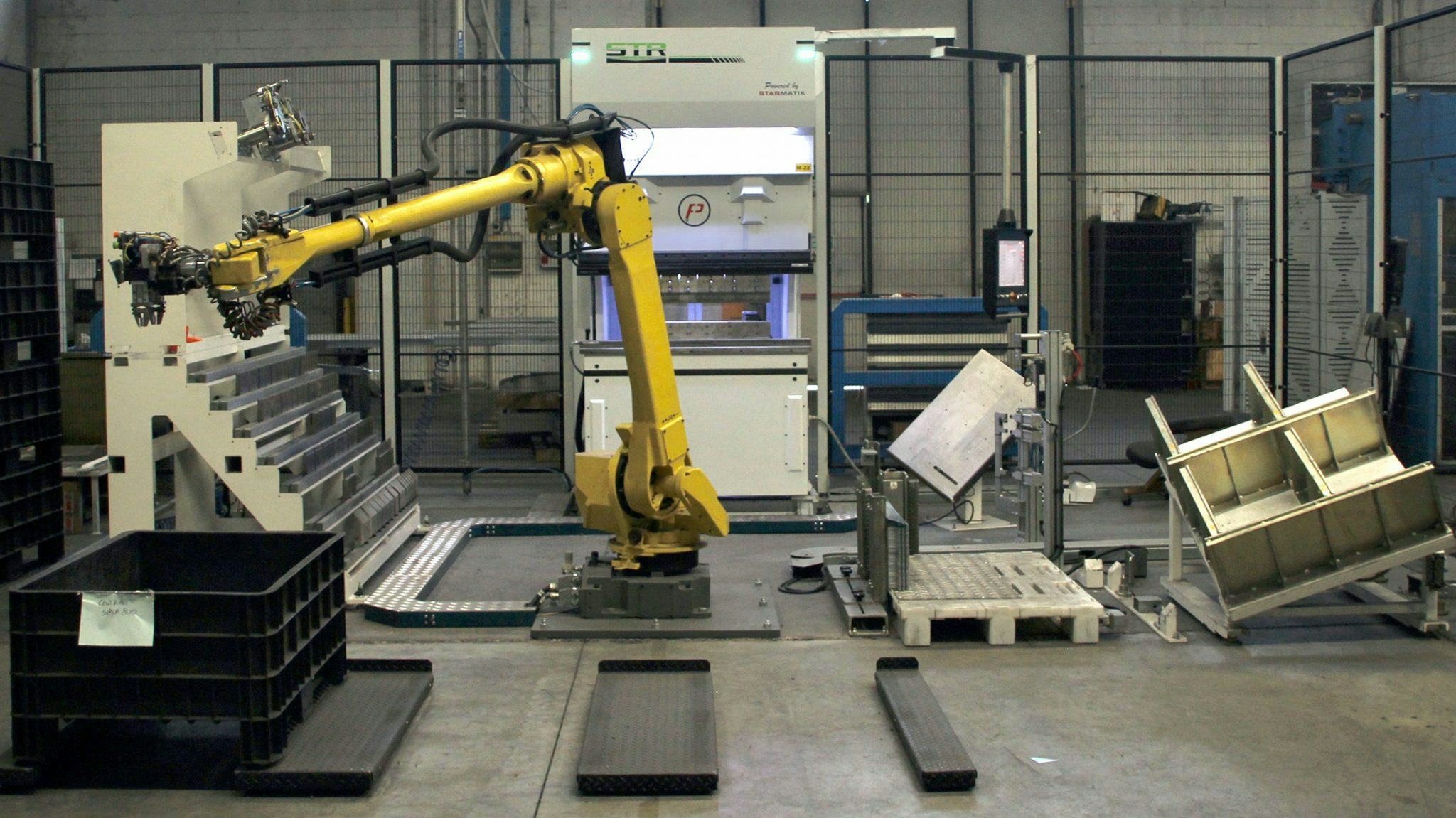
Factory setup of the automatic press brake bending machine.
Preziosa Francesco SRL’s existing gripper design was too slippery, reducing the accuracy of the end product. The gripper’s size and lack of agility also increased the risk of the machine stopping during operation. Lastly, manufacturing the grippers was a slow process that would take more than two weeks if outsourced.
The solution
Re-design robotic grippers for additive manufacturing
Add-it used nTop to re-design the grippers for additive manufacturing. They used metal 3D printing in 17-4 PH stainless steel with Desktop Metal’s Studio System so they could quickly produce metal parts in-house.
A reusable design process enabled the team to modify the design quickly and adjust it to the specific needs of each manufacturing job. This way, the team could create a reusable, end-to-end digital manufacturing workflow.
The results
70%
reduction in time to application
4
design variations in 1 afternoon
8%
weight reduction
35%
cost reduction compared to outsourcing
Why nTop?
nTop’s topology optimization enabled Add-it to design grippers that were both small enough to fit in the system without causing it to malfunction, and optimized to handle more delicate tasks. nTop also made it possible to develop reusable workflows that enabled Preziosa Francesco to easily update the gripper design.
Topology optimization
Add-it used nTop’s built-in topology optimization to generate a gripper with optimized geometry. The new gripper enabled the system to perform more delicate robotic operations and handle smaller metal sheets.
“We estimated the space we needed to save in the volume of the clamps. It was a matter of a few millimeters. Still, it was a few millimeters that counted in this application,” Rossi notes.
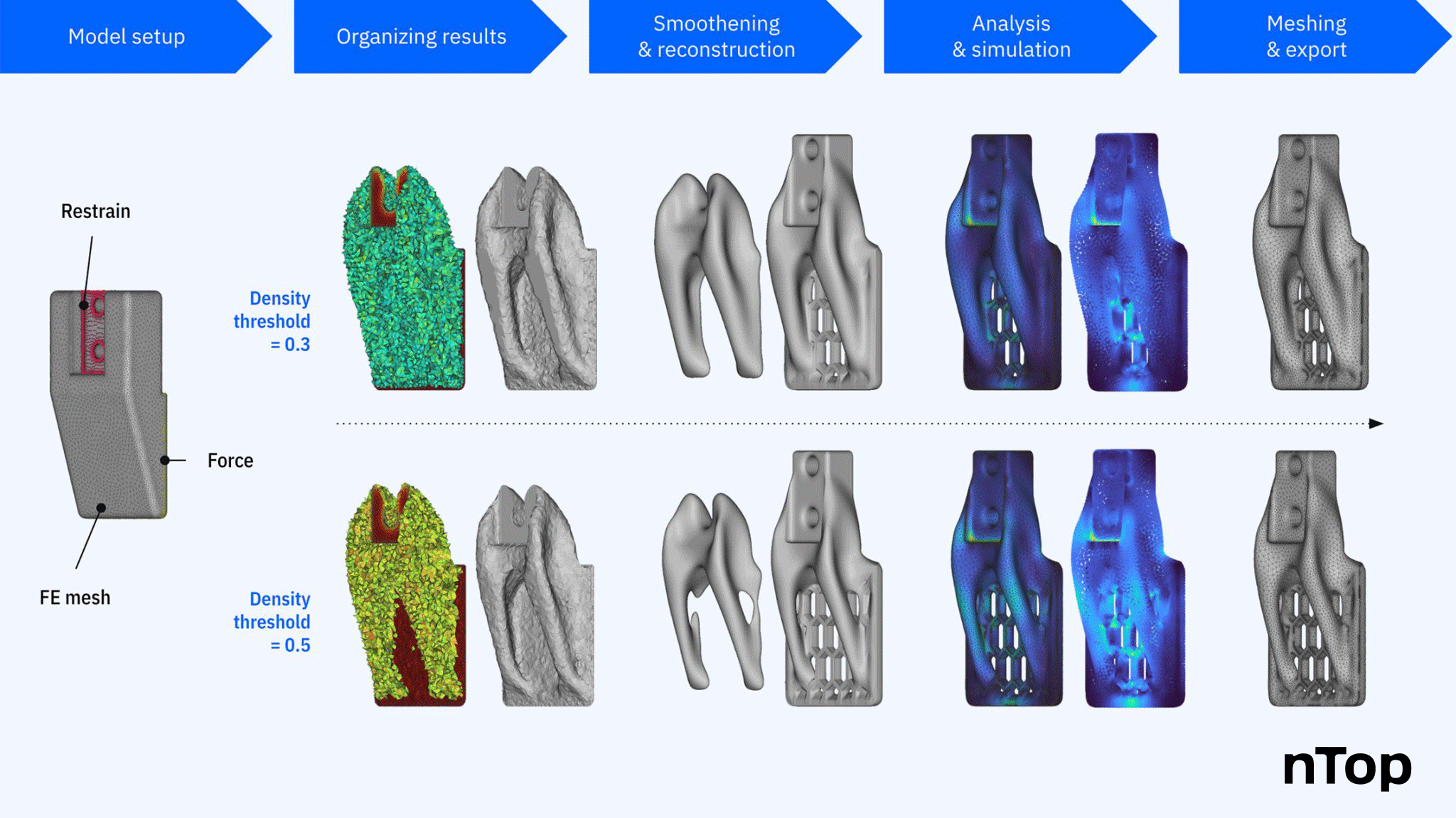
Overview of the fully-automated post-topology optimization design workflow in nTop.
Reusable design processes
The redesigned gripper greatly improved process reliability. By eliminating steps, it unlocked lights-out manufacturing and the full use of their additive manufacturing system.
Additionally, the ability to produce the parts they need in-house in a few days enables Preziosa Francesco SRL to adapt their system on short notice and easily update their processes when necessary.
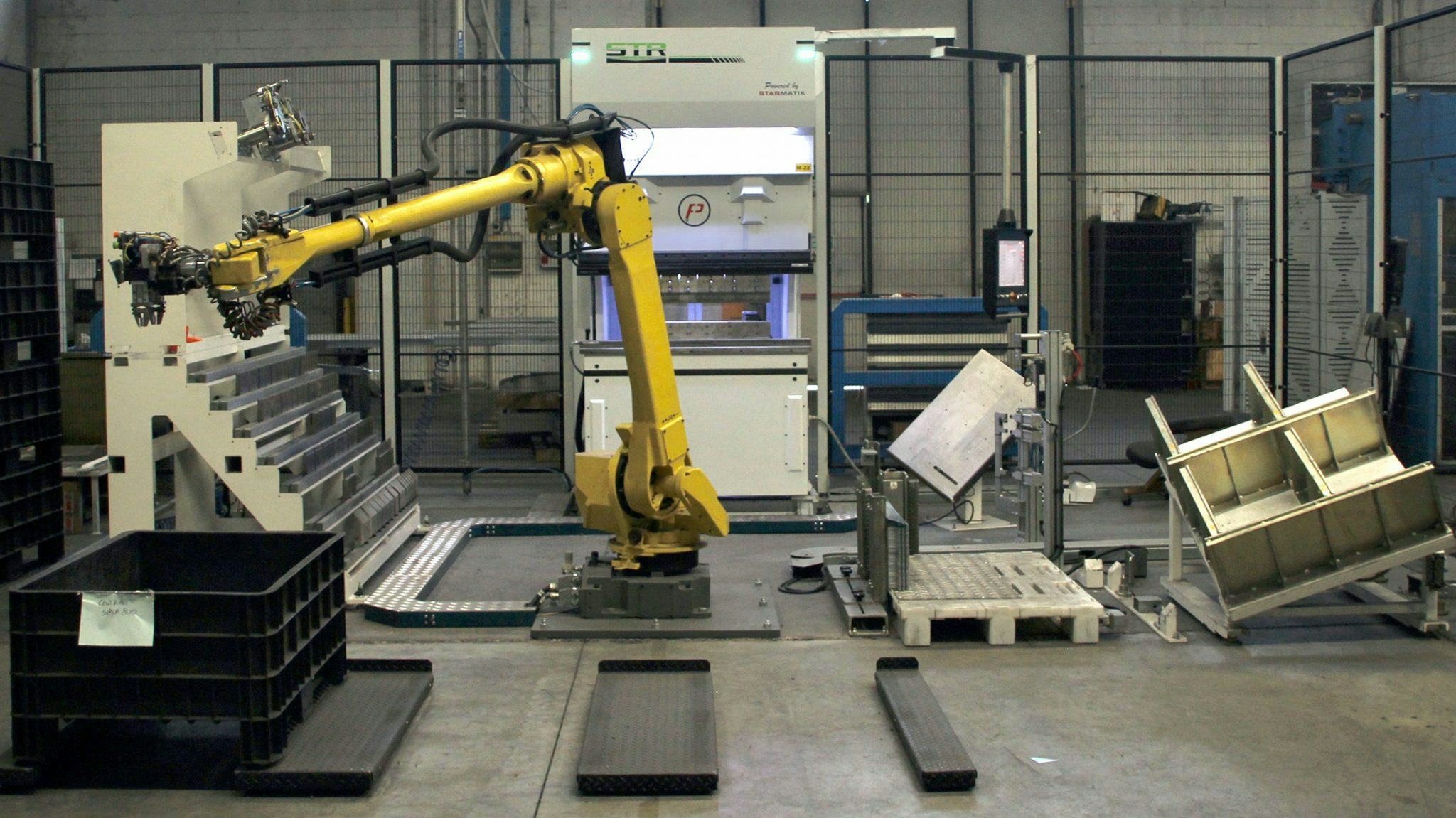
Factory setup of the automatic press brake bending machine.
Conclusion
nTop enabled Preziosa Francesco SRL and Add-it to create an end-to-end design and digital manufacturing process that produces custom robot grippers optimized for the job and takes advantage of the latest design methodologies — like topology optimization.
Related content
- CASE STUDY
Replacing spacecraft supermaterial with high-performance lattice
- VIDEO
Creating a computational design workflow to lightweight drone panels with nTop’s new ribbing tools
- WEBINAR
Accelerating Product Engineering with Computational Design
- VIDEO
nTop Siemens Energy at CDFAM NYC 2024
- CASE STUDY
Reducing weight to help win and withstand the rigors of a 24 hour Le Mans race