IMR and Renishaw streamline the additive manufacturing of spinal implants

Applications
Key Software Capabilities
- Design automation
- Lattice structures
Summary
IMR and Renishaw cut spinal implant design time down from a few days to a few hours with field-driven design and reusable workflows.

About: Irish Manufacturing Research (IMR) is a leading manufacturing research and technology firm. They offer manufacturing research services to industries ranging from chilled water systems to implantable medical devices.
- Industry: Medical devices
- Size: 10-50 employees
- Location: Dublin, Ireland
- Product: 3D-printed Anterior Cervical Interbody Device (ACID)
The project
Design custom lightweight spinal implants at scale
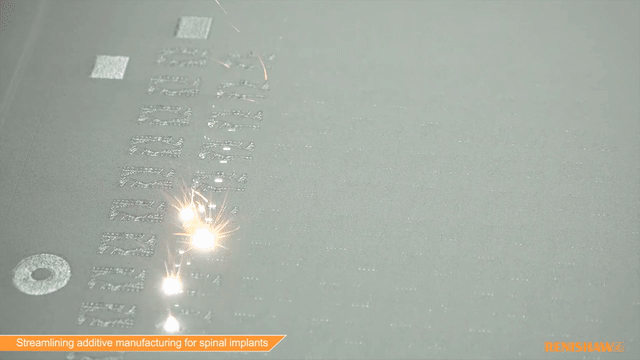
IMR used nTop to streamline the manufacturing process of spinal implants.
The goal was to create a spinal implant that could help restore intervertebral height in patients suffering from conditions such as degenerative intervertebral disc disease, vertebral fusion, spondylolisthesis, herniated disc, osteoporosis, and spinal stenosis.
The implants needed to mimic the material properties of bone and be quick to manufacture. Surgeons also had to be able to fix these implants in the vertebral column.
The challenge
Create a quick and controllable design process

The new implant is easier to print thanks to field-driven design and reusable workflows.
Designing these implants quickly would be challenging using legacy software. Controlling the many aspects of implant design under one workflow was going to be difficult, and optimizing various parts of the implant would exponentially increase the design time.
The solution
Optimize the implants using Field-Driven Design and reusable workflows
IMR and Renishaw used nTop to create efficient optimization workflows and controllable design processes that output designs ready for additive manufacturing.
The result was the rapid development of a spinal implant that improves patient outcomes in conditions where intervertebral height is compromised.
The final design has two distinct regions: a solid region with a fixed structure and a lattice region with a variable design optimized in nTop.
The results
Minutes
Instead of hours design time
Years
Saved in project time
95%
Reduction in output file size
Certified
ISO 13314, ASTM 1104, ASTM 1147
Why nTop?
nTop gave IMR the high degree of control necessary to make precise design changes and reduce risk. Reusable workflows helped the team iterate quickly without wasting time on repetitive tasks. Additionally, the ability to share direct-to-slice files reduced the communication time between nTop’s design platform and Renishaw’s manufacturing platform.
Faster design cycles
IMR developed seven concepts that went through the complete design cycle, with multiple iterations in each design cycle. The number of individual parts in these spinal implant devices could be anywhere between 20 and 100. nTop saved time by letting them develop a single workflow for all the parts and by facilitating easy reuse of existing workflows.

The final spinal implant design installed in an anatomical model.
Streamlining slicing and manufacturing
IMR exported designs directly to the native file format used by Renishaw’s build preparation software (QuantAM). Renishaw’s software directly translated the slices and contours generated in nTop into a laser toolpath and (ultimately) the error-free 3D-printed implants.

The spinal implants were additively manufactured in a Renishaw RenAM 500M Selective Laser Melting system.
Control key design variables
nTop provided control over which parts of the design were modifiable and which had to remain fixed. The engineering team could also trace the entire design process, which allowed them to track the various parameters used in previous iterations of the implant design. These features of the software helped reduce risk in the design phase.
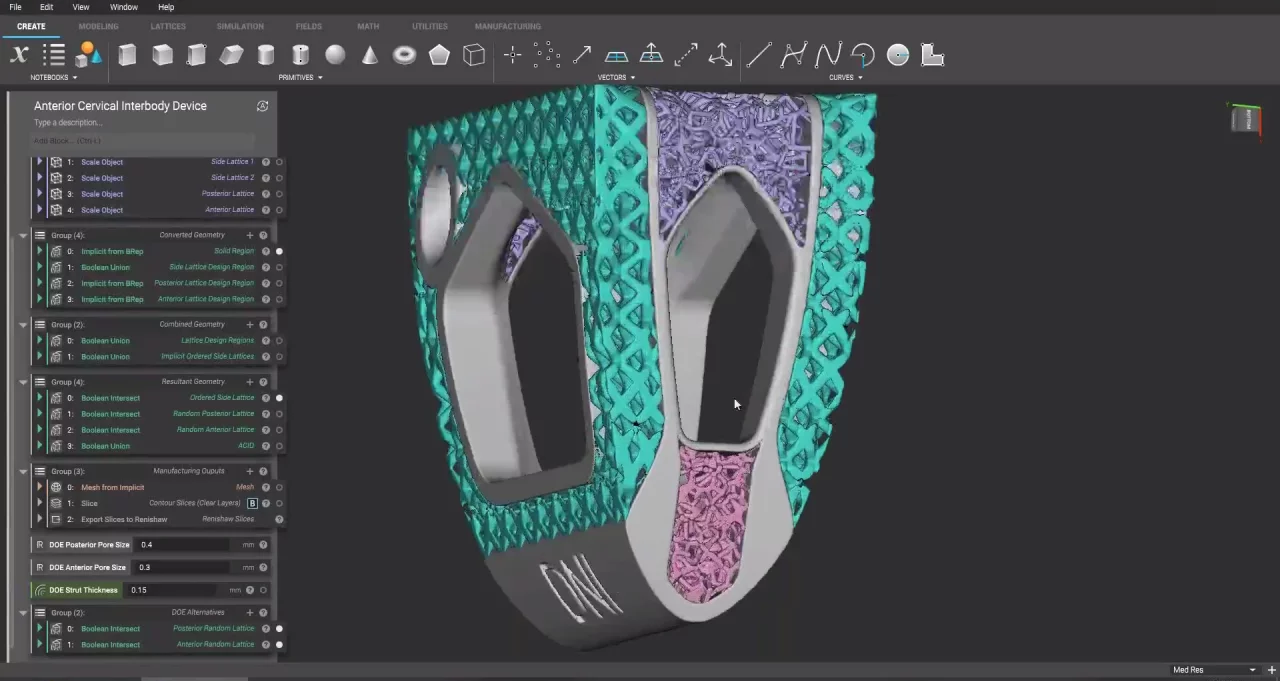
The final spinal implant design generated in nTop.
Conclusion
Using nTop, IMR and Renishaw streamlined the design and manufacturing process of 3D-printed spinal implants, and created a reusable workflow that saved significant engineering time. This collaboration highlights how additive manufacturing and nTop can make innovative, custom implants scalable.