Additively manufactured high-performance heat exchangers
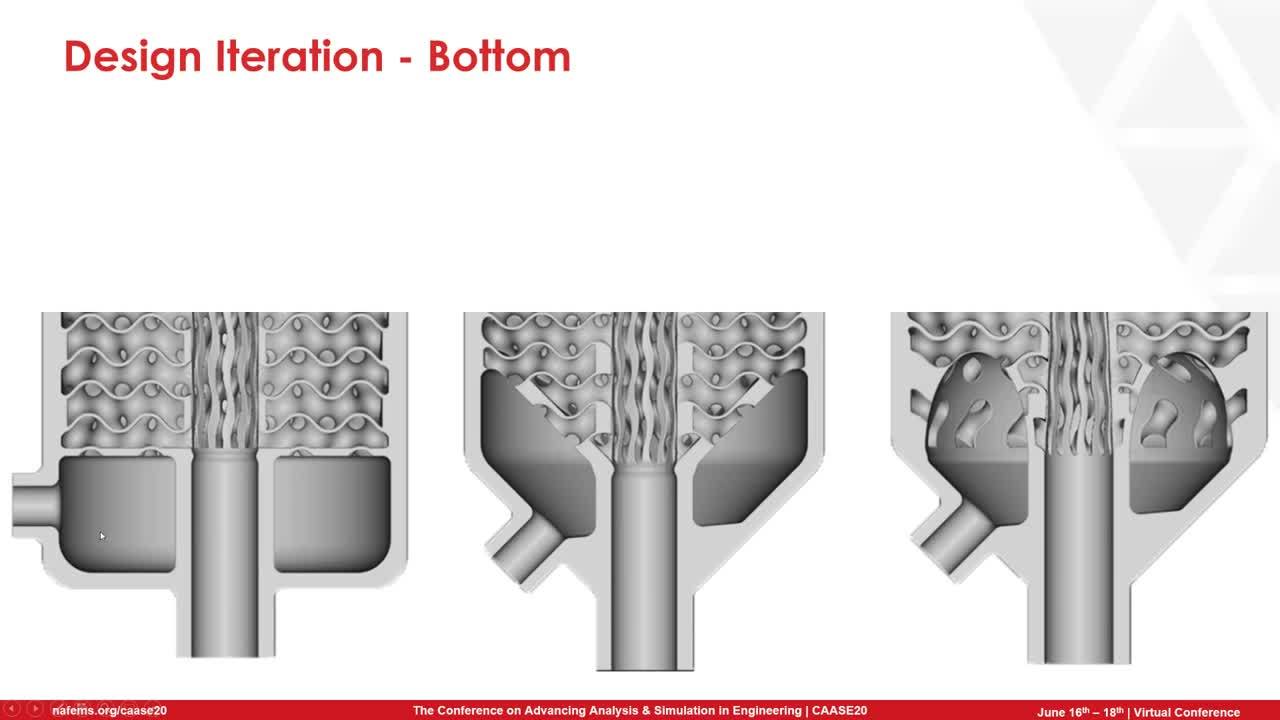
video of additively manufactured high-performance heat exchangers
Published on June 19, 2020
Combine the advanced geometry capabilities of nTop Platform with state-of-the-art CAE and CFD tools, like Ansys, to design high-performance heat exchangers. In this presentation, Maiki Vlahinos, Senior Application Engineer at nTop, describes the simulation-driven methodology he followed to improve the performance of an advanced heat exchanger by 300%; specifically, a Fuel Cooled Oil Cooler for aerospace applications. He argues that TPMS structures, such as gyroids, are an excellent candidate for this use-case because they:
- Separate a single volume into different, independent, and continuous regions
- Provide a large surface area for the minimum amount of material within a defined boundary
- Reduce pressure drop by smoothly merging the two independent regions
- Require no support structures during the additive manufacturing process
To access the files used during this session, click here.
This presentation was initially recorded at the CAASE20 conference.
Related content
- CASE STUDY
Replacing spacecraft supermaterial with high-performance lattice
- VIDEO
Creating a computational design workflow to lightweight drone panels with nTop’s new ribbing tools
- WEBINAR
Accelerating Product Engineering with Computational Design
- VIDEO
nTop Siemens Energy at CDFAM NYC 2024
- CASE STUDY
Reducing weight to help win and withstand the rigors of a 24 hour Le Mans race