CFD driven heat exchanger fin orientation, spacing and sizing
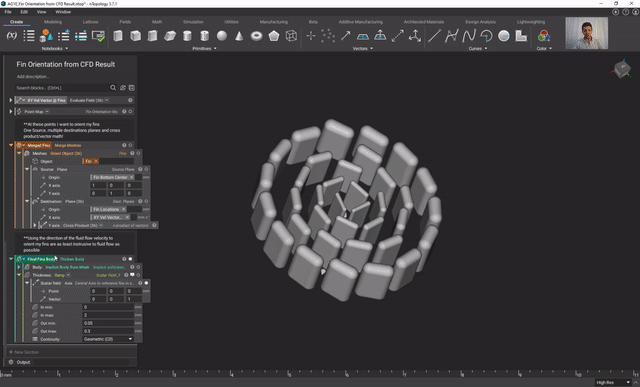
video:
Published on August 9, 2021
Applications
Key Software Capabilities
- Field Optimization
Using CFD data and a Field-Driven Design approach, you can directly alter the liquid flow in a high-performance heat exchanger to generate a flow path of least resistance that minimizes losses.
In this nTop live, Alec Guay, Application Engineer at nTop, walks you through a workflow that takes as input a CFD file and uses the vector component to orient fins that “go with the flow” instead of being evenly spaced and oriented along a wall. He then takes it a step further to alter fin thickness using fields and the Ramp nTop block.
Watch and learn how to:
- Import CFD data in nTop to drive feature orientation
- Change feature sizing and spacing using fields
- Use a Ramp block to control and smoothly alter fin thickness
Download the files
Recreate the steps that Alec followed in this nTop Training. To download all the necessary files for this training, please see this link.
Related content
- VIDEO
nTop 2025 Nvidia GTC Presentation
- VIDEO
When your design changes, how fast can you respond?
- CASE STUDY
Replacing spacecraft supermaterial with high-performance lattice
- VIDEO
Creating a computational design workflow to lightweight drone panels with nTop’s new ribbing tools
- WEBINAR
Accelerating Product Engineering with Computational Design