Computational design of performance-driven heat sinks
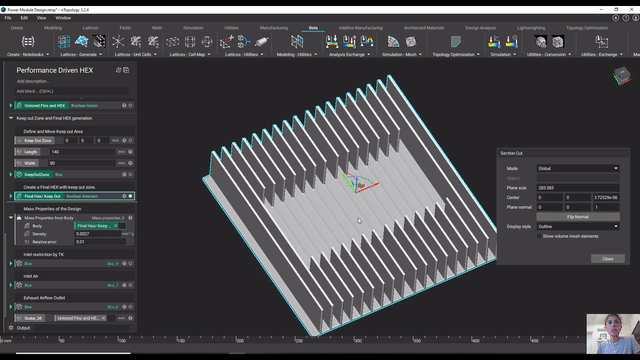
video: Computational design of performance-driven heat sinks
Published on June 3, 2021
Applications
Key Software Capabilities
- Field Optimization
- Design automation
The power of computational design is that you can use underlying physics equations to drive geometry and hit performance targets. By combining this key benefit with a Field Driven Design approach, you can create truly optimal designs.
In this nTop Live, Gabrielle Thelen, Application Engineer at nTop, shows you how to set up a fully parametric design workflow to generate performance-driven, power module heat sinks. She uses straight and sinusoidal wave fins to increase surface area while maintaining the desired heat sink’s footprint.
Watch and learn how to:
- Use equation & math blocks to generate designs based on analytical sizing
- Control geometry using Field Driven Design to create optimized heat sinks
- Link variables together to build a truly parametric, performance-driven workflow
Download the files
Recreate the steps that Gabrielle followed in this nTop Training. To download all the necessary files for this training, please see this link.
Related content
- VIDEO
nTop Siemens Energy at CDFAM NYC 2024
- CASE STUDY
Reducing weight to help win and withstand the rigors of a 24 hour Le Mans race
- ARTICLE
An nTop intern’s experience: Learning computational design and creating a lightweight drone
- VIDEO
Thermal Applications - The Hot Topics
- CASE STUDY
How blueflite reduced fuselage mass 25% in 4 hours instead of 4 weeks