Shell and tube heat exchanger: Made better with additive manufacturing
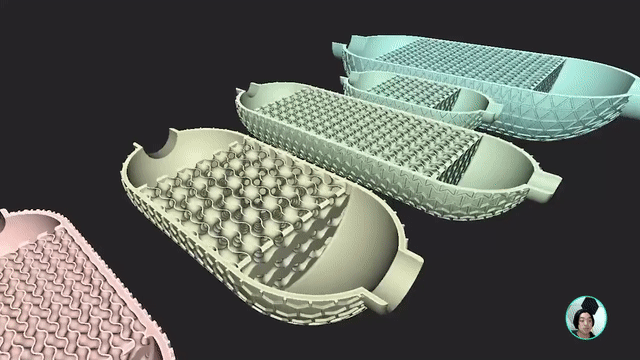
video: Shell and tube heat exchanger: Made better with additive manufacturing
Published on June 7, 2022
Applications
Key Software Capabilities
- Lattice structures
Shell and tube heat exchangers are one of the most common types of industrial heat exchangers. They have a simple design, high fluid flow and heat transfer rates, but they typically require more space than a plate heat exchanger.
In this nTop Live, Yuki Okada, Technical Marketing Engineer at nTop, shows you how to design a fully customizable heat exchanger that is optimized for Additive Manufacturing and has the same form factor as a traditional shell and tube heat exchanger.
He uses a gyroid TPMS structure for the heat exchanger core which has ideal properties for thermal management applications. He also adds ribs to the outer shell to increase the stiffness of the part. Lastly, he condenses the entire workflow into a reusable block to quickly go through multiple design iterations of the heat exchanger.
Watch and learn how to:
- Create a custom shell and tube heat exchanger design replacement
- Generate a two-fluid domain heat exchanger core using gyroid TPMS structures
- Package the entire process into a reusable workflow to iterate and optimize your design
Download the files
Recreate the steps that Yuki followed in this nTop Live. To download all the necessary files for this training, click here.