Simulation series - Topology optimized carbon fiber PP parts are "taking-off"!
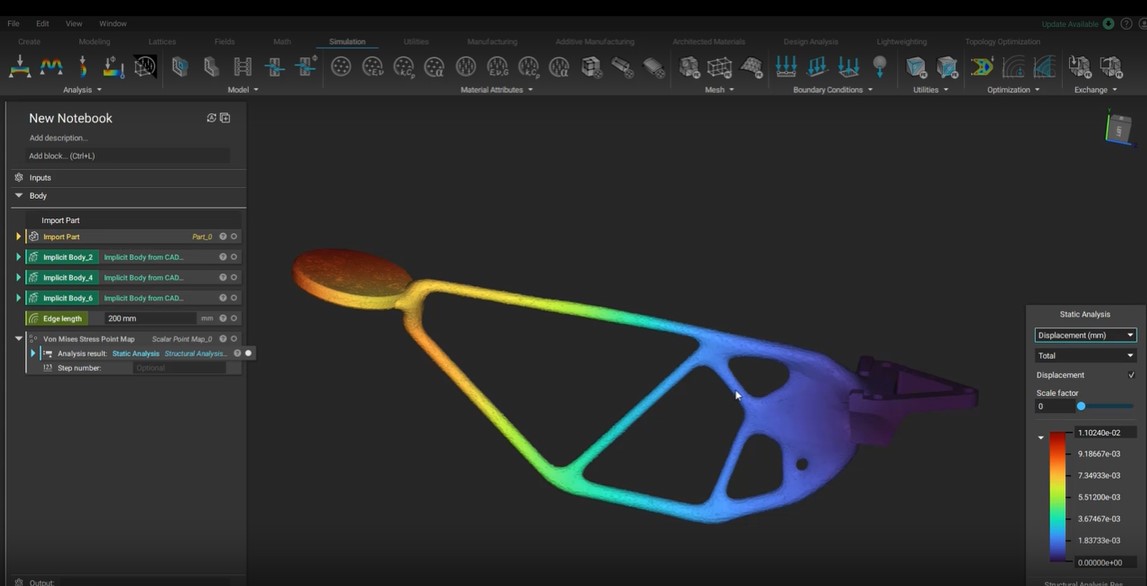
video: Simulation series - Topology optimized carbon fiber PP parts are taking-off!
Published on March 9, 2021
Applications
Key Software Capabilities
- Simulation
Jake Fallon, Braskem
There is vast opportunity to improve product performance in many industries when we begin to divert our thinking from traditional manufacturing limitations. Today’s pioneering technologies in digital design, advanced materials and next generation processes, together provides exceptional opportunities.
The example part we will explore is a topology optimized drone arm which is 3D printed with carbon fiber/polypropylene. We will investigate how the constraints for this application were defined, and how topology optimization and materials were used to reduce weight and improve strength. Simulation will compare the how the design and material optimization leads to greatly improved performance.
Key takeaways:
- Design optimization and material optimization work together synergistically to greatly improve performance
- Additive manufacturing allows for the unique organic structures created by topology optimization to be fully exploited.
- Mechanical simulation provides essential performance comparisons
Related content
- VIDEO
nTop 2025 Nvidia GTC Presentation
- VIDEO
When your design changes, how fast can you respond?
- CASE STUDY
Replacing spacecraft supermaterial with high-performance lattice
- VIDEO
Creating a computational design workflow to lightweight drone panels with nTop’s new ribbing tools
- WEBINAR
Accelerating Product Engineering with Computational Design